High voltage insulators play a critical role in the transmission and distribution of electricity, but their performance can be severely impacted by environmental pollution in contaminated regions. Various types of pollution such as ocean spray, salt fog, cement dust, and airborne agricultural dust can cause insulator flashovers. This occurs when dry-band arcing leads to leakage currents and results in a breakdown of the insulation.
In this article, we explore four ways to mitigate insulator flashovers. While each method has its advantages and disadvantages, investing in long-term solutions like RTV coatings can ultimately save on maintenance and repairs in the future.
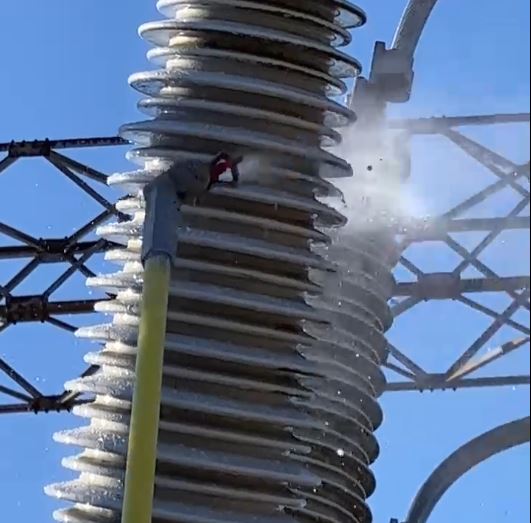
Washing Or Blasting
Frequent cleaning is the most common method to keep an insulator running safe and efficiently. This process involves spraying demineralized water or blasting organic material on the surface of the insulator, removing most contaminants to reduce the risk of flashovers.
While water washing is a great method to maximize system performance, there are safety and damage concerns, especially during energized washing. Additionally, it can rack up enormous expenses over the life of the insulator if pollutants accumulate regularly.
Application Method
Wash by hand or via insulated spray wand attached to a pump or blast pot.
Increase Creepage Distance
Creepage extenders have been used to prevent pollution flashovers on insulators for over 20 years. These extenders are sealed to porcelain or glass insulators, driving the high leakage currents found in polluted areas around the edge of the extender’s skirt. This can help to reduce the risk of flashovers by increasing the surface path over the insulator.
However, this method only postpones the inevitable fact that the insulator will continue to accumulate contaminants and require cleaning. Flashovers may still occur during long periods of no rain and high humidity.
If extenders are not applied properly and leave gaps, then electricity will find its way through, rendering it ineffective.
Application Method
Glue or seal to insulator by hand.
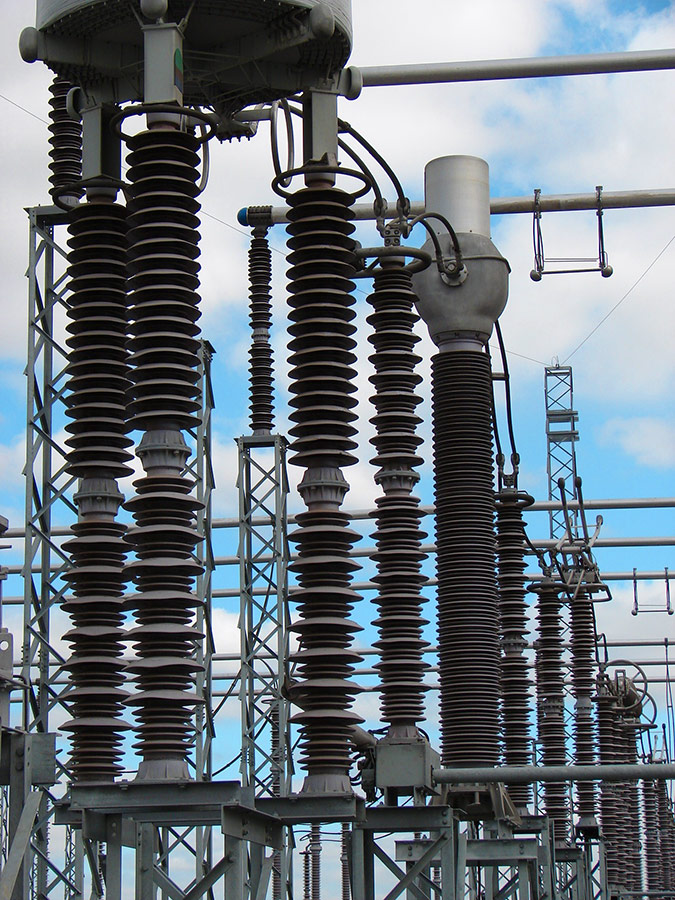
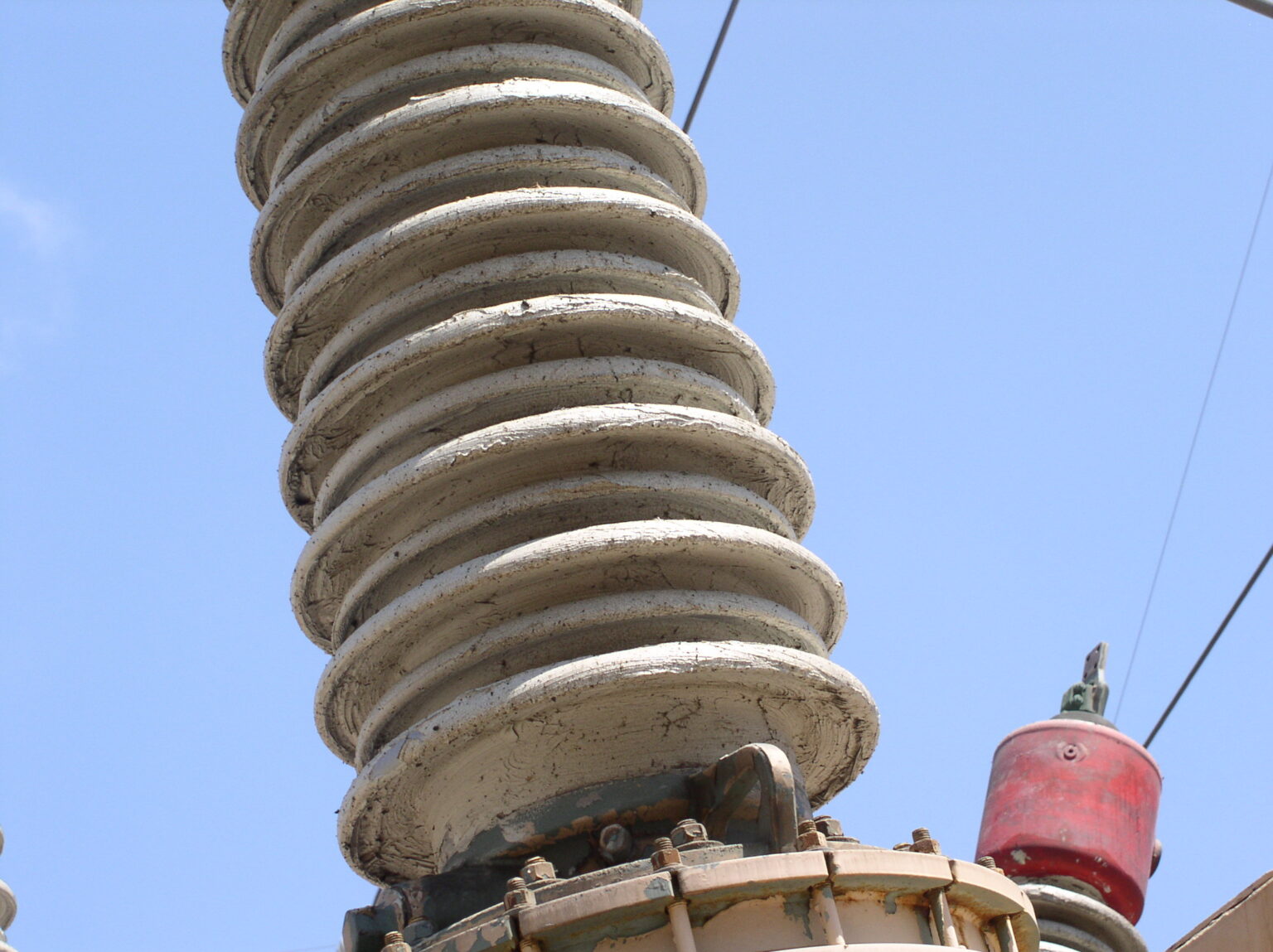
Silicone Grease
Silicone grease is one of the original solutions to insulator protection since the 1960s with good initial results in preventing the effects of pollution on the insulator’s surface.
Silicone grease is:
- Water-repellent
- Is not water soluble
- Arc track-resistant surface encapsulates pollutants
- Results in a lower lifetime cost than washing only
However, within a couple years in service:
- It becomes saturated with contaminants
- Requires aggressive and tedious removal and reapplication
The messy use of silicone grease, while at one time effective before advanced materials became available, is now being discontinued practice worldwide.
Application Method
Apply by hand or brush on.
Silicone RTV Coatings
Silicone Room Temperature Vulcanization (RTV) coatings create a self-cleaning protective rubber layer over the high voltage insulator to protect it from the environment .
RTV coatings work by creating a hydrophobic surface that prevents water absorption and coats the contaminant particles, rendering them hydrophobic. This reduces the contaminants’ ability to combine with water to form an ionic solution.
This silicone coating is the most competitive solution over the long-term providing:
- Arc track resistance
- Excellent UV resistance
- Superior adhesion
- Wide temperature stability
- Lasting hydrophobicity
Application Method
Apply via spray, brush, or dipping. The coatings are usually cured at room temperature, making it easy to apply them in the field.
While the initial cost of an RTV coating may be higher than other methods, the long-term maintenance and repair costs are significantly lower, making it a cost-effective solution over a long-term period.
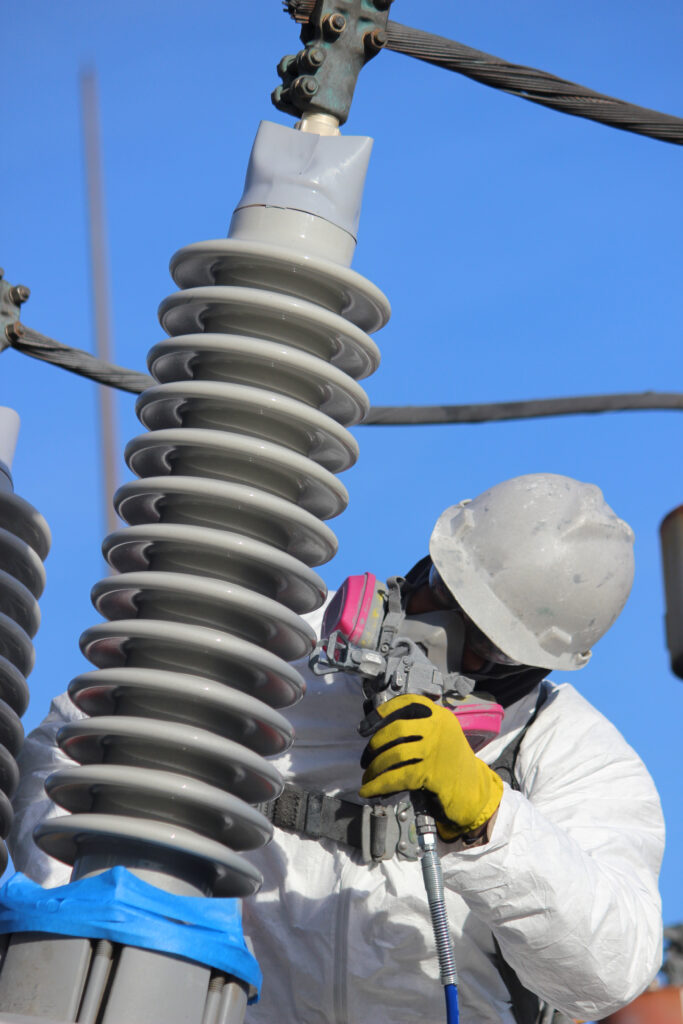
Other Ways to AVOID FLASHOVER
In addition to these four methods, there are other ways to reduce the risk of flashovers including:
- Routine inspections can help to identify and remove contaminants before they can cause arcing and leakage currents.
- Using insulators with larger surface areas can also help to reduce the risk of flashovers by spreading the voltage across a larger area.
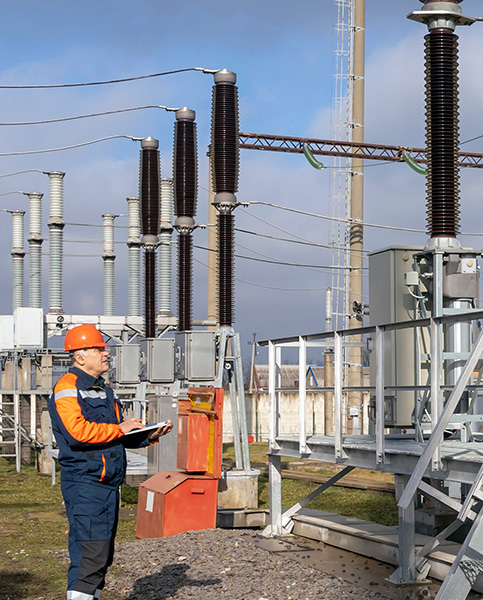
The possibility of a flashover is a serious concern for those who work around high voltage insulators.
By taking measures to mitigate the effects of environmental pollution on the insulator’s surface, you can reduce the risk of flashovers and improve system performance.